プロジェクトストーリーMISSION
創業以来培ってきた確かな技術力と強固なチームワークを武器に、時代やお客様のニーズに応えながら挑戦・進化を繰り返してきた新貝工業。ここでは新貝工業が手掛けた大型案件の1つを例に挙げ、実際に携わった関係者に当時のエピソードを語ってもらいます。
MISSION
上越火力発電所の
建屋と煙突を結ぶ
超巨大排気ダクトを完成させる。
中部電力が新潟県上越市の直江津港に建設した上越火力発電所。その建屋と煙突を結ぶ最大100mにもおよぶ排気ダクトの製作を依頼された新貝工業。これまでの社歴の中でも最もスケールが大きく、高い技術力を求められるものだった。ミスや妥協が許されない中、”チーム新貝”は英知を結集して8本のダクトを無事に完成させた。
MEMBER
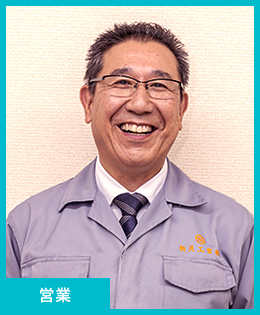
宮川 俊也常務取締役(当時営業部)
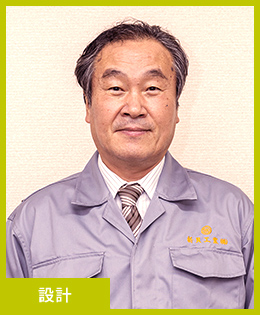
白田 進設計部
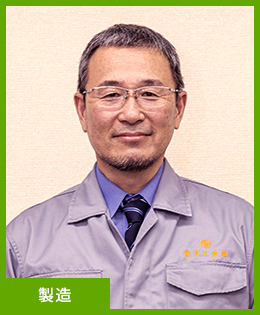
新貝 政彦製造部 現場工場長
01
経験と発想力が導いた
“パネル化”構造
宮川 | 取引先であるI社へ型枠の営業に伺った時に、「新貝さんのところでこんな物は作れませんか?」と図面を見せられたのがこのプロジェクトのはじまり。火力発電所建設の仕事に携わりたいとは思っていましたが、正直始めは不安でした。 |
---|---|
白田 | 私も話を聞いた時は面白そうだと思った反面、これだけの規模の物を形にする設計提案ができるか心配でしたね。 |
新貝 | サイズにしてもスケールにしても当社の歴史の中で一番でしたもんね。 |
白田 | これまでは5メートル四方に長さ10~12メートルの一体物のダクトを、現地でつなげて箱にしていくという手法でした。ですがその構造だと大き過ぎて陸送ができない。営業担当だった常務と当時の社長(現相談役)と私の3人で何度も策を練り、1つのダクトを分割してパネル化することはできないかと考えました。 |
宮川 | 発電所建設地の近くに当社所有の空き地があったので、パネル化を実現できれば工場でパーツを作製して現地で組み立てることが可能となります。 |
白田 | ハブメーカーのB.H社も従来の構造にはサイズや重さを含め危険性を感じていたようで、当社の提案を好意的に受け取ってくれました。パネル化という新たな構造設計を採用していただいた時はうれしかったですね。 |
宮川 | 営業担当としては話が進むにつれて不安も大きくなってきて…。何しろ今までに経験したことのない仕事量と金額だったので。設備投資だけで数千万円でしたし(苦笑)。ですが当社の技術力とノウハウがあれば成功できる自信があったし、この挑戦は会社の財産になると思いました。I社からも「全力でバックアップするので一緒に頑張りましょう」と心強い言葉をいただき、前に進むことを決断しました。 |
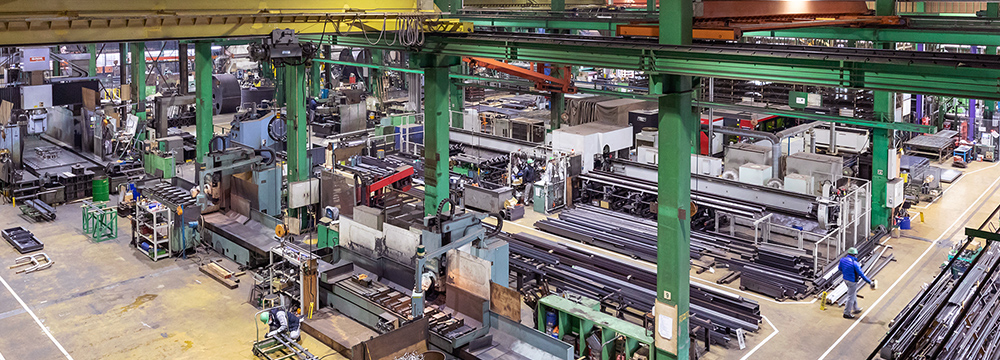
02
ルールの違いに戸惑いながらも、
準備の大切さを実感
宮川 | 設計案が決まって、現場設備に取りかかったのが2008年。本格的な工事を開始したのが2010年ごろからだったので…準備にもだいぶ時間を要したよね。 |
---|---|
新貝 | まず、作業現場が当初予定していた当社所有の土地から火力発電所構内に変更になったね。 |
白田 | そうそう、我々の作業場の目の前に中部電力さんの事務所があったんです。現場はかなり気を遣いましたよね。 |
新貝 | 常に監視されてる気がして(笑)。あと、何よりも現場における法律や安全対策などが製造業と土木業では異なるので、そこはかなり困惑しました。当社としては製造業のルールに基づいて作業するつもりだったのに、いざ現場に入ると土木のルールに従わないといけなくなって。 |
白田 | 最初にクレーンを設置する際も、基礎がどの程度必要かなどのエビデンスが厳しく求められました。うちは鉄工所なので、土木関係の知識は全くなかった。異業種の知識をいちから習得することは簡単ではありませんでしたが、クレーンが据えてある現場へ見学に行ったり地耐力の計算方法を学んだりしながら一歩ずつ課題を解決していきました。 |
宮川 | 設計部・製造部が一丸となって安全に製作するための仮設設備を設計。B.H 社や中部電力からも了承を得ることができました。準備が整ったら次は生産ライン整備の設計を。 |
白田 | 足場を移動式にするといった工夫を施すなど、現場のルールに沿って作業手順を考えましたね。また、仮組みしたダクトを反転させる作業もここで行うためシミュレーションを何度も繰り返しました。 |
新貝 | 初めて現地で反転作業を行った時は見物客もたくさんいらして。皆さん注目してましたよね、よく覚えています。 |
白田 | なんせ重さ約25トンですから。仮にここで失敗したら作業がストップしてしまいますし、お客様や協力会社に「新貝工業大丈夫かな…」という印象を与えてしまいますので。 |
宮川 | 我々も含めてそこにいた全員がドキドキの瞬間だった。うまくいった時はホッとしたよね。紆余曲折もあったけど、ようやくすべての設備が整い作業前の準備が完了。長かったよね。 |
新貝 | 準備段階からこんなに大変で大丈夫かなと思いましたよ。常務がおっしゃった通り現場設備で2年近くかかりましたもんね。 |
白田 | 当時はこの場から逃げ出したい気分でした(苦笑)。でもこういった大きな仕事をする時はスタート前の準備がいかに重要なのかをつくづく感じました。まぁ自分自身も勉強になりましたし、今振り返ってみればいい思い出です。 |
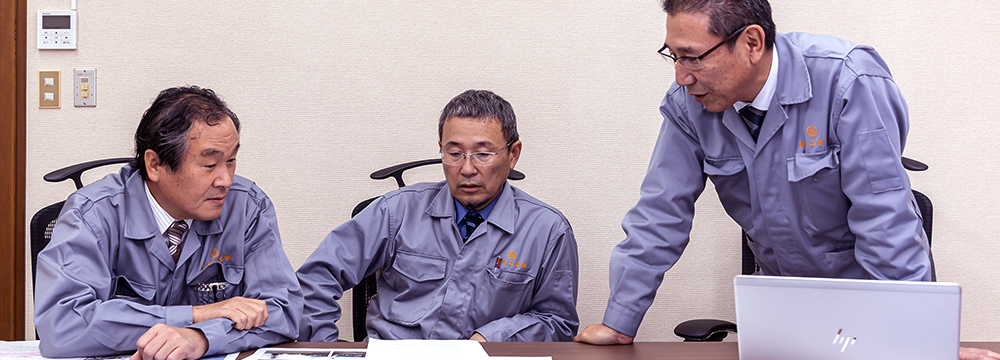
03
問題やプレッシャーに打ち勝った、
固い絆とチームワーク
宮川 | 実際に生産が始まってからも問題は山積みだったよね。現場監督としてのプレッシャーもすごかった? |
---|---|
新貝 | 土木ルールの中での作業だったので、始めは探り探り。なかなか予定通りに進まず工程も少しずつ遅れていきました。それに加えて現場作業は天候にも左右されてしまう。この年は特に暑い日が続いて、熱中症にも注意しないといけなかった。 |
白田 | 海沿いとはいえ現場の周りには何もないですもんね。かといって風が強いと溶接不良などにもつながるし。 |
新貝 | 風を防ぐためにビニールを張るといった対策を講じていましたが、溶接現場は蒸し風呂状態でしたよ。それでも慣れていくにつれてスタッフのパフォーマンスも上がってきました。あと、本社工場が現場から近いということも良かった。工場スタッフを人員投入することで臨機応変に対応し、スケジュールの遅れを取り戻しましたね。もう一つ、大きな問題となったのが、支給された部品の品質。取り付け作業には中国製の部品を使用していたのですが、ボルトが合わないなど図面通りに製品が出来上がらない。これには相当手を焼きましたね。 |
宮川 | 普段、中国製の部品を使用していないので、品質の良し悪しまでは把握していなかった。ボルトが斜めに向いちゃってたりね。 |
新貝 | はい、そもそも頭が六角形じゃなかったりする物もありました(苦笑)。部品の不備は自分たちで修正しながら使っていたのですが、その分時間も手間も余計にかかりました。 |
白田 | それと、天候に関していうと、台風の時季とかは雨風がすごくて。足場が崩れたり、25トンもある鉄の塊のダクトが動いたりしたこともありましたよね。部品の件もそうですが、想定外のことが次々と起こりました。 |
新貝 | 当社の現場スタッフは私を含めて10名ぐらいだったのですが、彼らが本当に良くやってくれました。団結力もより一層高まりましたよ。 |
宮川 | 最後の据え付け作業も力が入ったよね。あの時はうちの本社工場で仮組をして間違いのないことを確認してから、現場で搬入・据え付けを行いました。 |
新貝 | 500トンクレーンを使用するなど、最後まで気の抜けない作業が続きました。これだけ多くの人が関わり、協力してここまできたので失敗は許されません。プレッシャーがすごかったです。煙突への繋ぎ込みがうまくいって1号機系列の工事が完了したのが2013年。合計8本のダクトを製作しましたが、すべての作業を終えた時は感無量でしたね。 |
04
挑戦で得た経験とノウハウを、
若い世代にも継承していきたい
宮川 | 工事期間が約3年、計画段階から含めると7年もの歳月がかかった大型プロジェクト。不安も大きかったけど、ひとつずつ壁を乗り越えながら完成までたどり着けて本当に良かった。 |
---|---|
白田 | 計画段階から参加させてもらい、知らないことだらけの中で多くの経験を積むことができました。発電所の心臓部であるタービン建屋の中に入るといった通常は味わえない貴重な体験もできましたし。 |
新貝 | 現場としては品質はもちろん、納期も守らないといけなかったので、毎日が必死でした。当社の仮設工場から取り付け現場へダクトを運ぶために大型のトラックドーリーがくるのですが、「まだ来ないでくれー」と思うことも。 |
白田 | タイヤが100個も付いているようなトラックですもんね。とにかく何もかもスケールが大きかった。 |
宮川 | またこういった機会があったら挑戦したいですか? |
新貝 | 設計・製造そして営業も含めて、まさに会社が一丸となってやり遂げた案件でしたね。今も時々発電所の前を通りますが、やっぱりカッコイイですし、胸を張って誇れる仕事です。 |
白田 | …(苦笑)。精神的にもかなりきつかったので…。 |
新貝 | でも若い社員たちにも経験させたいですし、挑戦を続けることが当社の社風。会社としてはこういった大型案件にも取り組んでいけたらと思います。 |
白田 | そうですね。今回の案件はこれまで先輩方が培ってきた信頼・実績・技術があったからこそ成し遂げることができました。私たちもこの経験やノウハウをしっかりと次の世代に繋いでいきたいと思います。 |
宮川 | 会社にとって大きな財産になりました。これからも全員が同じ方向を向いて、地域・社会に貢献するようなモノづくりに励んでいきたいですね。 |
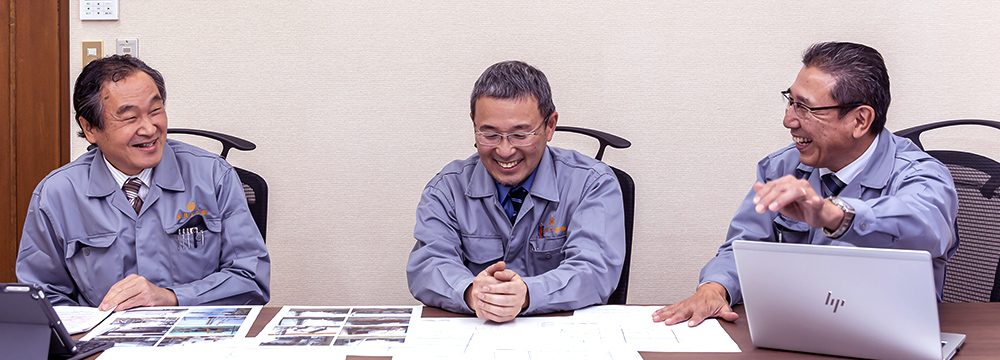